brigitte-doll.de
Diese Domain steht zum Verkauf - starten Sie jetzt durch!
Domain-Experte
Leo Kobes
"So gute Domains sind heute nur noch selten auf dem Markt erhältlich. Diese Gelegenheit ist einmalig. "
Domain-Experte
Leo Kobes
"Eine qualitativ hochwertige Domain wie diese ist ein tolles Marketinginstrument für Unternehmen - online sowie offline. "
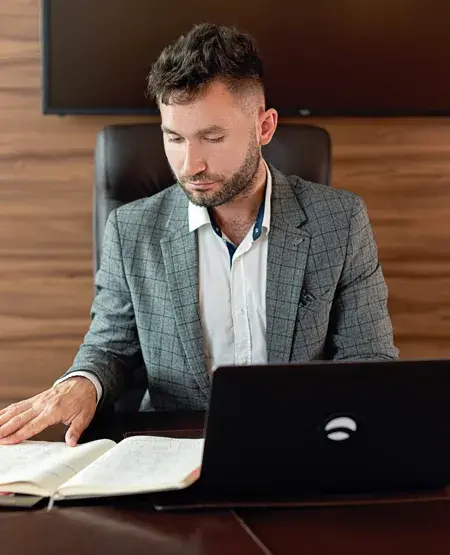
-
1
Domain auswählen
Sie klicken einfach auf "Domain kaufen" und übermitteln uns anschließend Ihre Daten.
-
2
Bezahlvorgang
Sie bezahlen einfach mit Kreditkarte (Paypal), Banküberweisung oder Sofortüberweisung.
-
3
Transfer der Domain
Sobald die Bezahlung erfolgt ist (oft innerhalb weniger Sekunden), wird Ihre neue Domain für Sie in einen eigenen Account verschoben und Sie erhalten die Zugangsdaten, um die Domain zu verwalten.
-
4
Loslegen!
Sie können Ihre neue Domain z.B. auf Ihre bestehende Homepage weiterleiten oder zu Ihrem aktuellen Provider umziehen (mittels Auth-Code).
So kaufen Sie eine Domain:
Sichere Zahlung
domainname.de übernimmt die komplette Zahlungsabwicklung. Mit 100 % Geld-zurück-Garantie, falls Sie Ihre Domain nicht erhalten.
Treuhändische Abwicklung
Alle Transaktionen werden von unserem Treuhandteam überwacht. Mit einem bisherigen Transfererfolg von 100 %.
Kompetentes Serviceteam
Unser Team begleitet Sie während der gesamten Abwicklung - vom ersten Kontakt bis hin zum erfolgreichen Transfer der Domain.